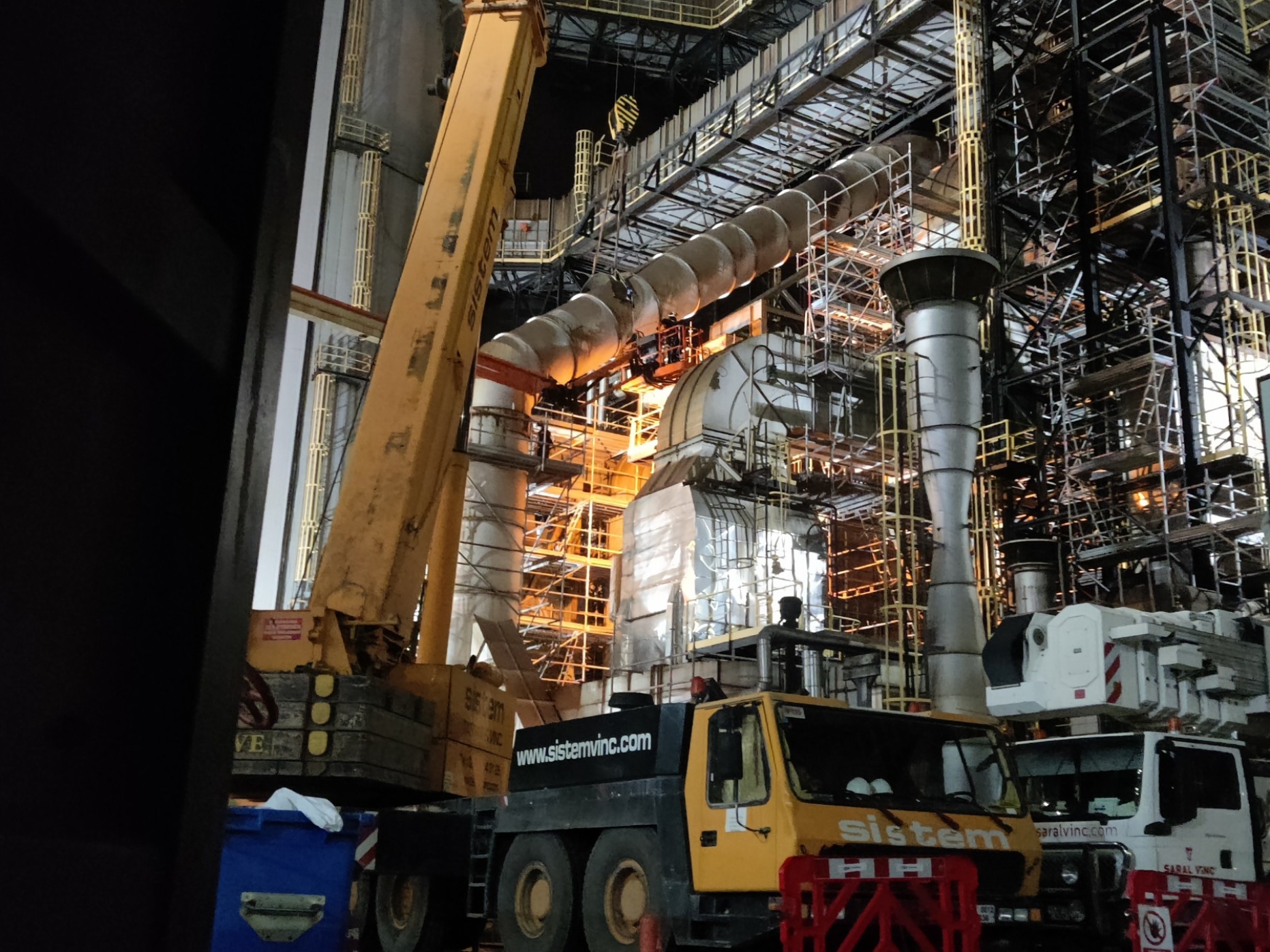
Furnaces in petrochemical plants are crucial for performing high-temperature chemical reactions, processing materials, and thermal treatments. Their operation, design, and maintenance are integral to ensuring efficiency, safety, and reliability in petrochemical processes. Here’s a detailed guide on furnace maintenance:
1. Types and Functions
- Pyrolysis Furnaces:
- Function: Used for thermal cracking or converting hydrocarbons, such as naphtha or gas oils, into valuable products like ethylene or propylene.
- Process: Operates at high temperatures and an oxygen-free environment to break down hydrocarbons into simpler compounds.
- Catalytic Reformer Furnaces:
- Function: Converts light petroleum products (e.g., gasoline) into aromatic hydrocarbons through catalytic reactions.
- Process: Involves high temperatures and the presence of catalysts to enhance the conversion process.
- Hydrocracking Furnaces:
- Function: Converts heavy hydrocarbons into lighter hydrocarbons, often using hydrogen.
- Process: Operates at high temperatures and pressures, with hydrogen added to facilitate the breaking down of heavy hydrocarbons.
- Thermal Cracking Furnaces:
- Function: Used for the thermal cracking of organic substances, obtaining basic components like carbon and hydrogen.
- Process: High temperatures in an oxygen-free environment to decompose complex hydrocarbons.
2. Working Principle
- High-Temperature Operation:
- Furnaces operate at elevated temperatures to facilitate chemical reactions or material changes. The specific temperature settings depend on the type of furnace and process requirements.
- Controlled Atmosphere:
- Some furnaces operate under vacuum or in an inert gas atmosphere (e.g., nitrogen or argon) to prevent unwanted reactions or to maintain process conditions.
- Thermal Processes:
- The furnace heating elements or burners generate the required heat. This heat is transferred to the process materials to initiate reactions or changes.
3. Application Areas
- Hydrocarbon Processing:
- Usage: In refineries to convert crude oil fractions into more valuable products, such as gasoline, diesel, and chemical feedstocks.
- Chemical Synthesis:
- Usage: For synthesizing or transforming chemical products, including the production of monomers like ethylene and propylene.
- Thermal Processing:
- Usage: In metalworking industries for hardening or shaping metal parts through high-temperature treatments.
4. Design and Safety
- Material Selection:
- Design: Furnaces are constructed using materials that can withstand high temperatures and corrosive environments. This ensures durability and efficiency in high-temperature operations.
- Safety Protocols:
- Maintenance: Regular inspections and maintenance are essential to prevent leaks, monitor the condition of heating elements, and ensure the accuracy of control systems.
- Insulation: Proper insulation is crucial for maintaining temperature control and preventing heat loss. Regular checks and maintenance of insulation materials are necessary.
- Performance Monitoring:
- Heating Elements: Regular checks of heating elements to ensure they are functioning correctly and efficiently.
- Control Systems: Monitoring and calibrating controls to ensure they are accurately regulating temperature and process conditions.
Maintenance Best Practices
- Routine Inspections:
- Perform regular inspections of furnace components, including heating elements, insulation, and control systems. Look for signs of wear, corrosion, or damage.
- Preventive Maintenance:
- Schedule and perform preventive maintenance tasks such as cleaning, component replacements, and calibration of controls based on the manufacturer's recommendations.
- Safety Checks:
- Ensure that safety systems, such as pressure relief valves and emergency shutdown mechanisms, are functioning properly. Conduct regular safety drills and reviews.
- Documentation:
- Keep detailed records of all maintenance activities, inspections, and repairs. This documentation helps track the condition of the furnace and supports future maintenance planning.
- Training:
- Provide ongoing training for maintenance personnel on the latest technologies, safety procedures, and maintenance techniques.
Proper maintenance of furnaces in petrochemical plants is essential for operational efficiency, safety, and product quality. By adhering to best practices and ensuring thorough inspections and maintenance, facilities can optimize their furnace performance and extend their operational lifespan.